When shopping for quick couplings, you may come across terms like “flow rate,” “maximum flow rate,” and “flow capacity.” While these terms might seem technical, they are crucial for ensuring that your quick couplings perform efficiently and meet your operational needs. In this blog post, we’ll break down what these terms mean, why they matter, and how to use them when selecting quick couplings for your specific applications.
What Is Flow Rate?
The flow rate refers to the volume of fluid (liquid or gas) that passes through the quick coupling per unit of time. It’s typically measured in liters per minute (LPM) or gallons per minute (GPM), though other units can also be used depending on the system’s needs. For example, in a hydraulic system, a flow rate of 50 LPM means that 50 liters of fluid flow through the coupling every minute.
The flow rate is an important specification because it helps you determine whether the quick coupling can handle the volume of fluid required for your equipment or machinery. If the coupling can’t accommodate the flow rate needed, it could lead to inefficiencies or damage to the system.
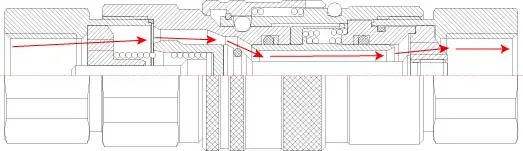
What Is Nominal Flow Rate?
The nominal flow rate is the typical or recommended flow rate at which the coupling operates most efficiently under normal conditions. It is the flow rate that the coupling is designed to handle regularly and is typically quoted in product specifications.
While the nominal flow rate reflects the ideal operating conditions, it’s important to note that this is not the absolute maximum capacity of the coupling. Instead, it is the flow rate that ensures optimal performance, balancing efficiency and longevity.
For example, a coupling with a nominal flow rate of 100 LPM is designed to perform most efficiently at that rate. Operating at higher or lower flow rates could impact performance, though the coupling can typically handle small variations above or below this rate without issue.
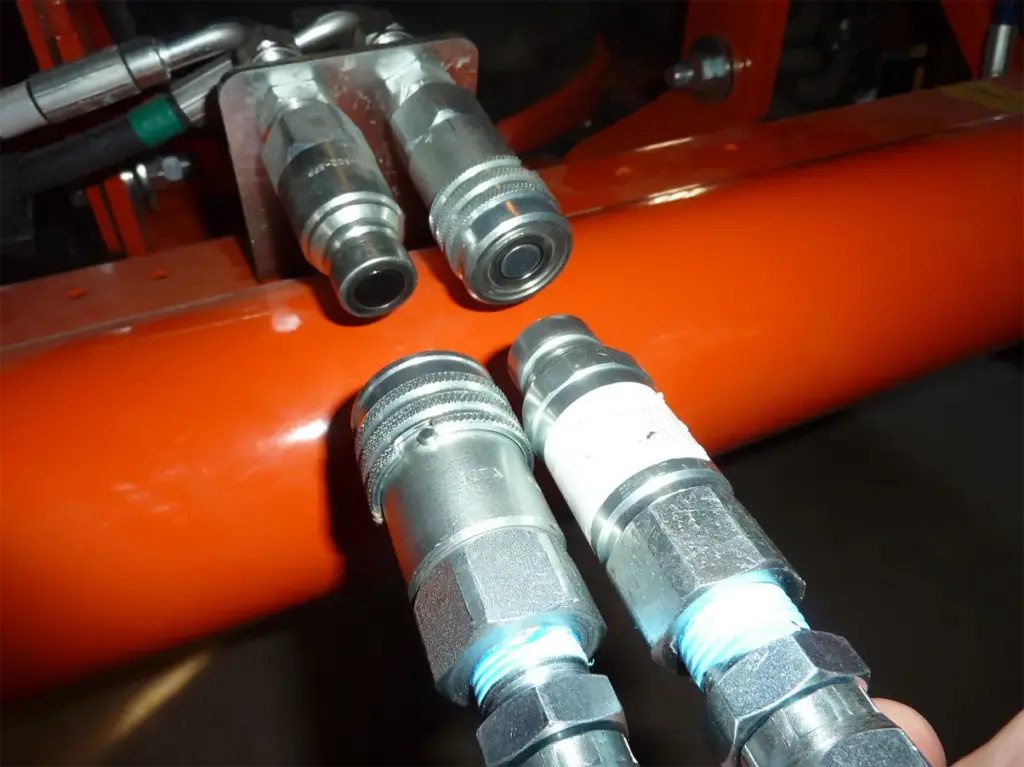
Maximum Flow Rate: Why It Matters
The maximum flow rate is the highest volume of fluid that the coupling can safely handle without being damaged or causing performance issues. Exceeding this rate can result in leaks, reduced performance, or even catastrophic failure of the coupling.
For example, a quick coupling with a maximum flow rate of 100 GPM is designed to handle up to 100 gallons per minute. If your system needs to flow more than 100 GPM, you’ll need to look for a coupling with a higher maximum flow rate.
Knowing the maximum flow rate of your quick coupling is essential to prevent overloading the coupling and ensure that your system runs smoothly and safely.
Pressure and Flow Rate: What’s the Connection?
Flow rate and pressure are closely related in any fluid-based system, including hydraulics. Pressure is the force pushing the fluid through the system, and flow rate is the volume of fluid moving through. The maximum pressure rating of a coupling tells you how much pressure the coupling can withstand, while the flow rate indicates how much fluid can move at that pressure.
If the flow rate is too high for a given pressure, the system could experience increased resistance, leading to pressure drops or inefficiencies. Conversely, if the pressure is too high for the coupling’s flow rate, it could cause wear and tear or even failure.
What Affects Flow Rate?
Several factors can affect the flow rate through a quick coupling. Understanding these factors can help you optimize your system:
- Internal Diameter: The larger the internal diameter of the coupling, the higher the flow rate it can handle. Smaller diameters restrict the flow, which can be beneficial in some applications but limit the overall capacity of the system.
- Material and Design: Different materials, such as stainless steel, carbon steel, or brass, have varying resistance to flow. Additionally, the internal design of the coupling, such as valve type or port configuration, can influence flow rates.
- Fluid Viscosity: Thicker fluids (higher viscosity) will flow more slowly than thinner fluids, which could affect the performance of the coupling. When working with viscous fluids, a coupling with a higher flow capacity may be necessary to maintain efficiency.
- Temperature: The temperature of the fluid can also impact its viscosity, and consequently, the flow rate. Hotter fluids tend to have lower viscosity, allowing them to flow more easily.
How to Choose the Right Flow Rate for Your Quick Coupling
When selecting a quick coupling for your system, it’s essential to match the coupling’s flow rate specifications with the requirements of your application. Here’s how you can choose:
- Determine the Flow Requirements: Understand the required flow rate for your system. This information can usually be found in the system’s design specifications.
- Choose the Correct Size: Ensure that the coupling’s internal diameter and flow capacity match or exceed the needs of your system.
- Consider Future Needs: If you expect the flow rate or system pressure to change over time, choose a coupling with a higher maximum flow rate to accommodate potential future upgrades.
- Match the Pressure Rating: Always ensure that the coupling’s pressure rating aligns with your system’s pressure needs, as exceeding either the flow rate or pressure could damage the coupling.
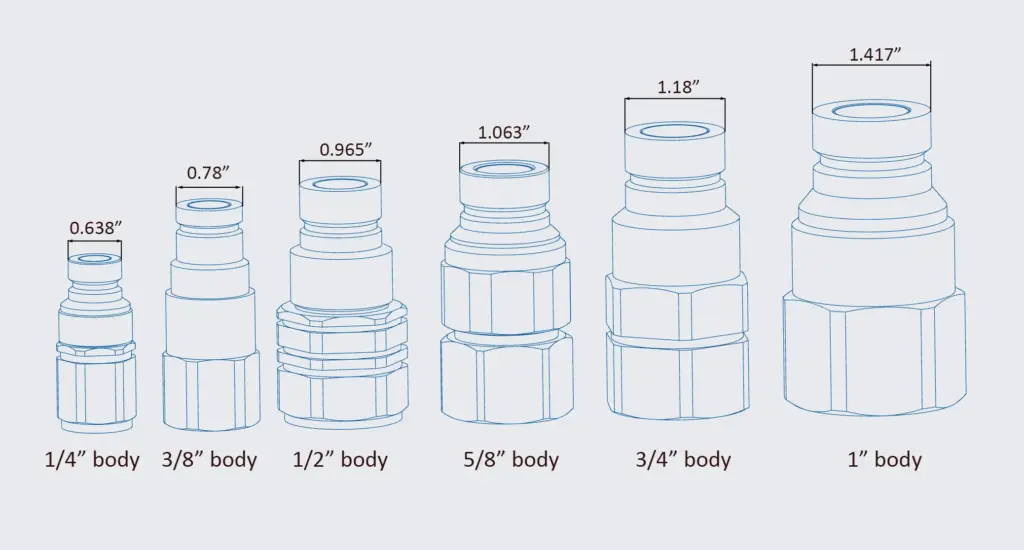
Conclusion
Flow rate, nominal flow rate, and maximum flow rate are crucial specifications to consider when selecting quick couplings for your system. Understanding these terms and how they impact performance will help you make informed decisions, ensuring that your quick couplings work efficiently and safely in your application.
Always choose a coupling that can handle your system’s required flow rate and pressure to ensure long-term performance and reliability. If you’re unsure about which coupling to choose, don’t hesitate to contact our team—we’re here to help you find the perfect solution for your needs.